Chemistry, Food and Pharma
IoT processes are in high demand in the chemical and pharmaceutical industries, as well as in the food industry. These processes require sensors, because states cannot be captured or actions carried out without them. KELLER Pressure is a leading manufacturer of pressure sensors, making it the ideal partner when it comes to implementing IoT solutions.
Filters
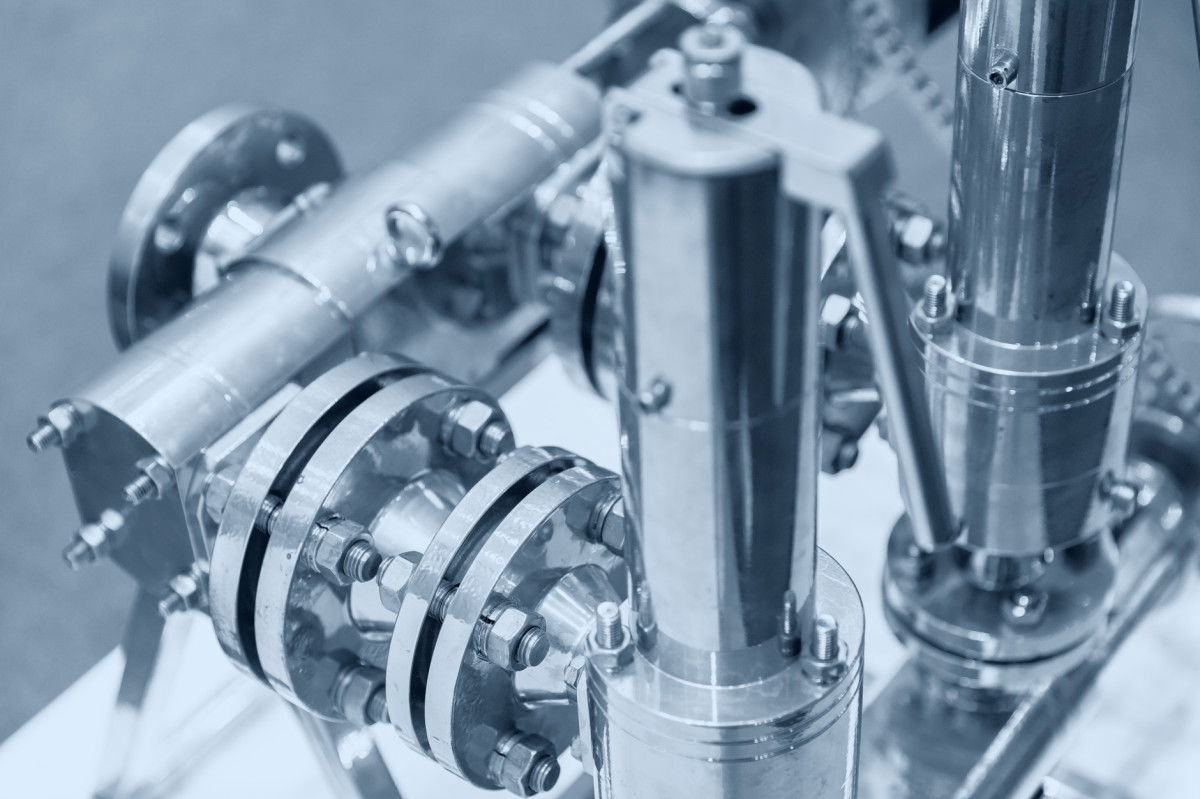
Pressure Control Means Outstanding Process Control
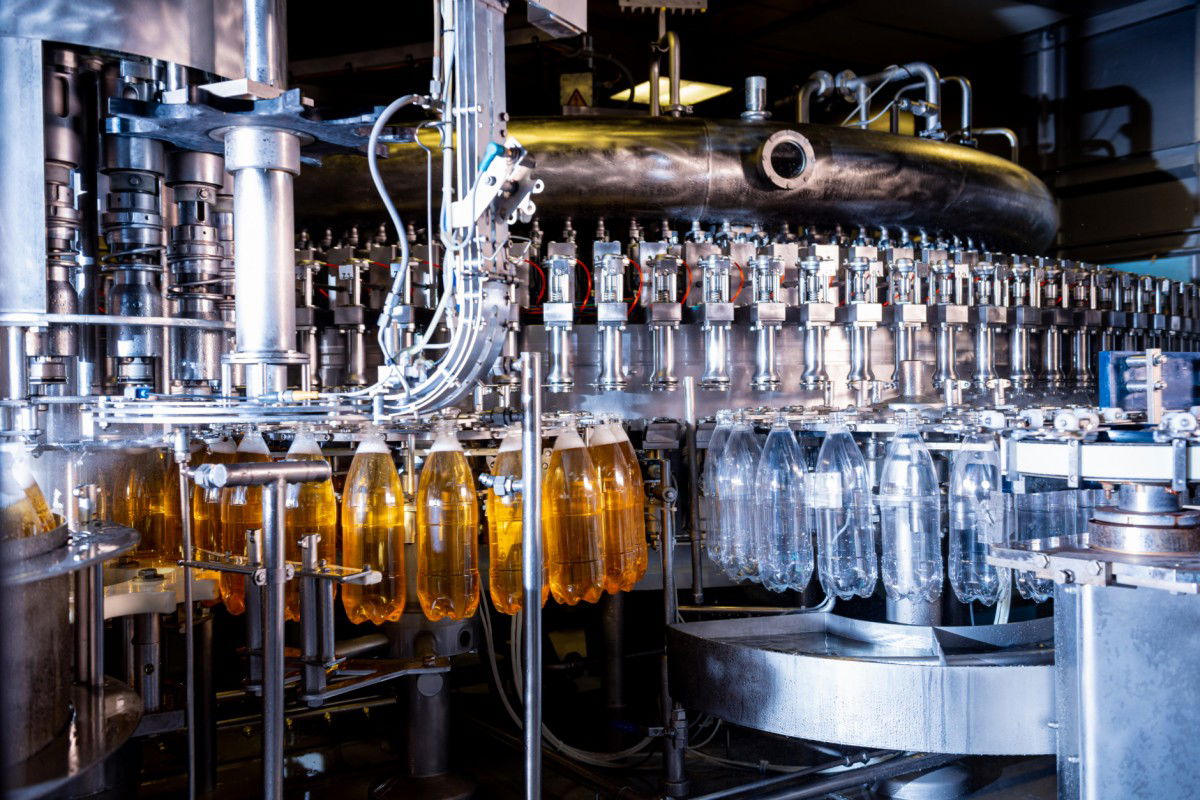
Sterilising Bottling Machines
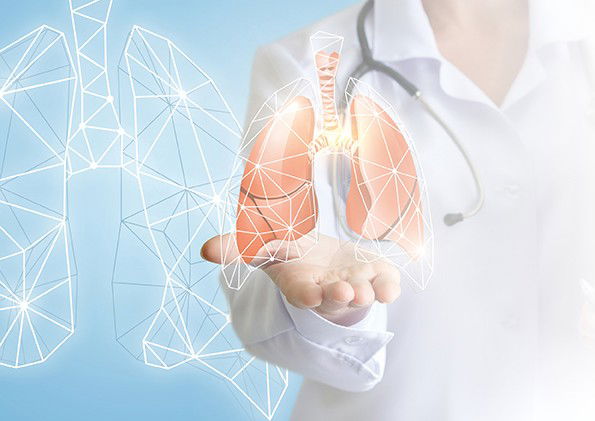
Management of Medical Oxygen
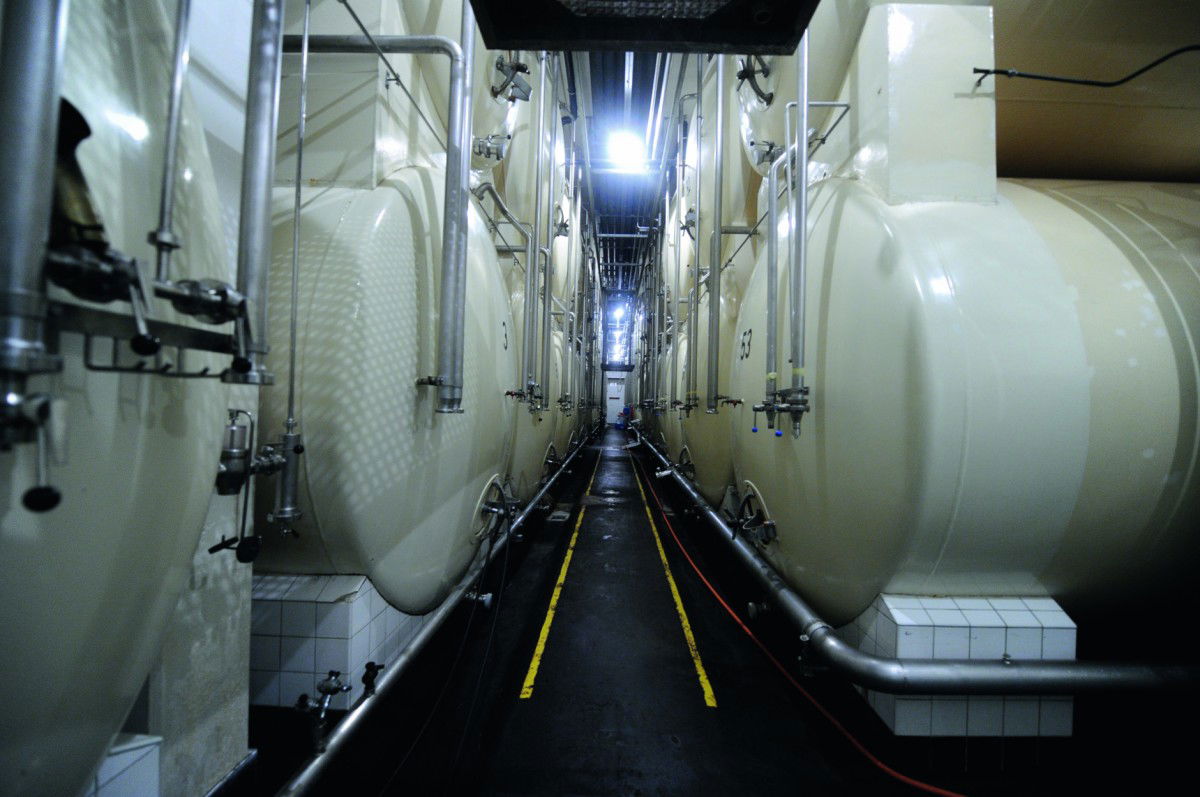
Networked Beer Tanks
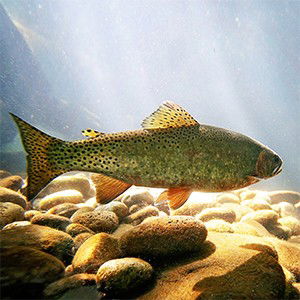
Fish Farm Water Level Monitoring
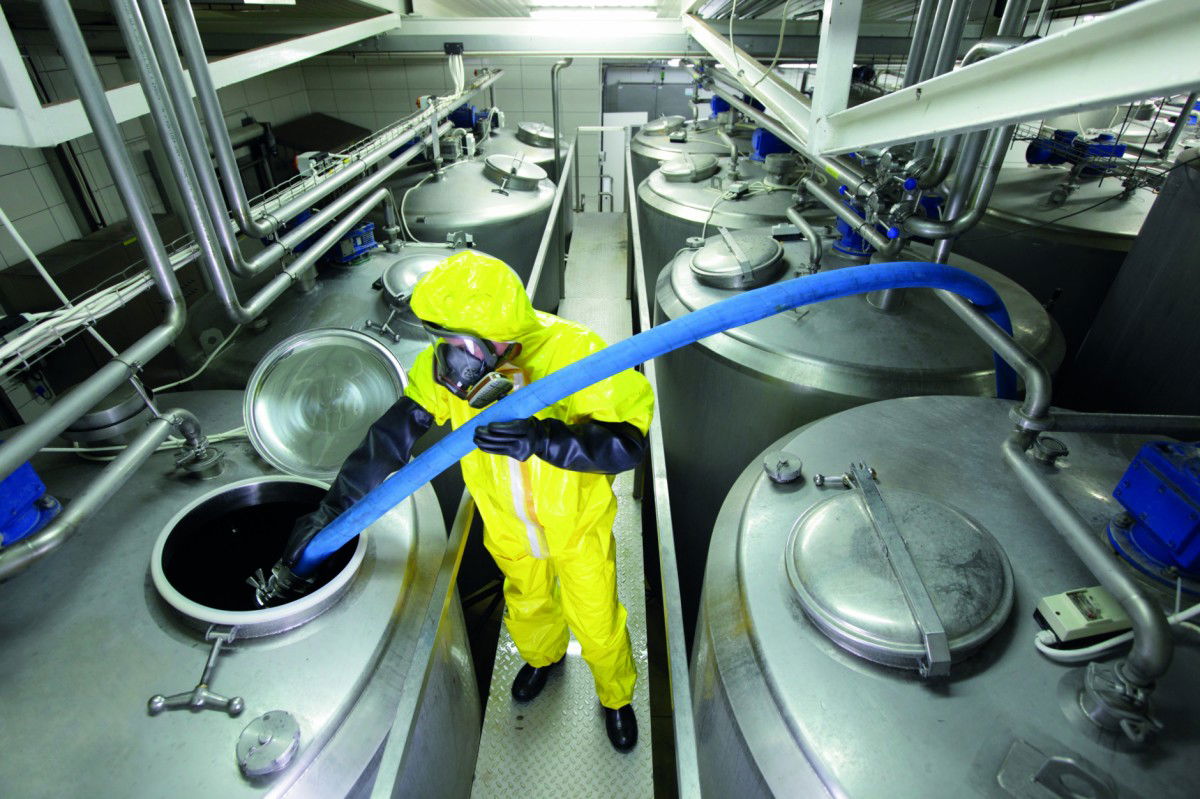
Chemical Distribution
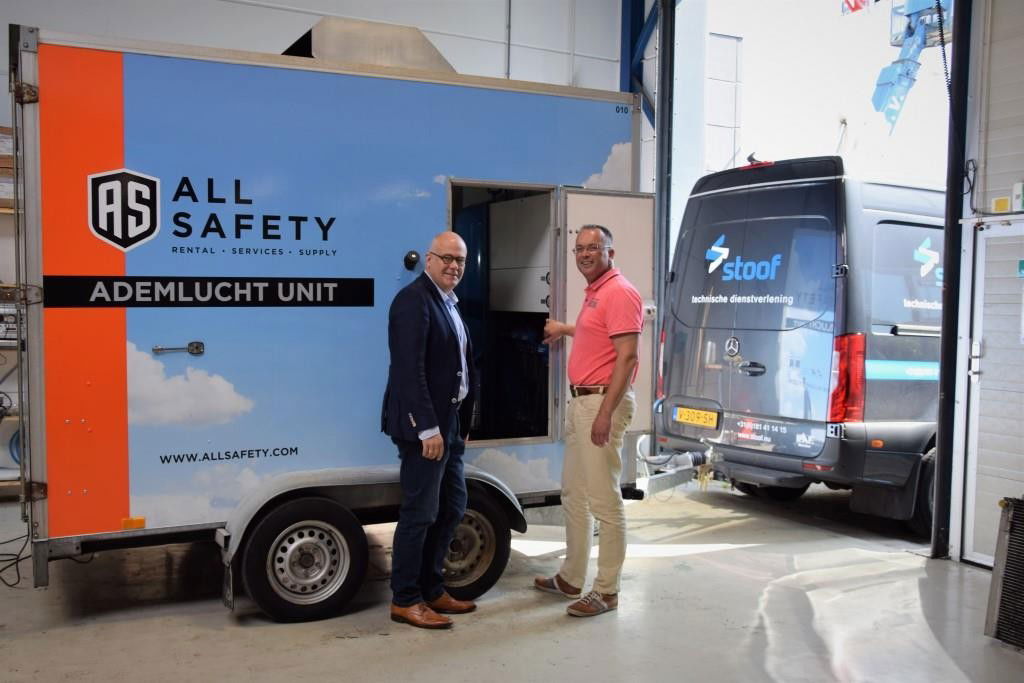
Digital Oxygen Valve

Steam Sterilisers
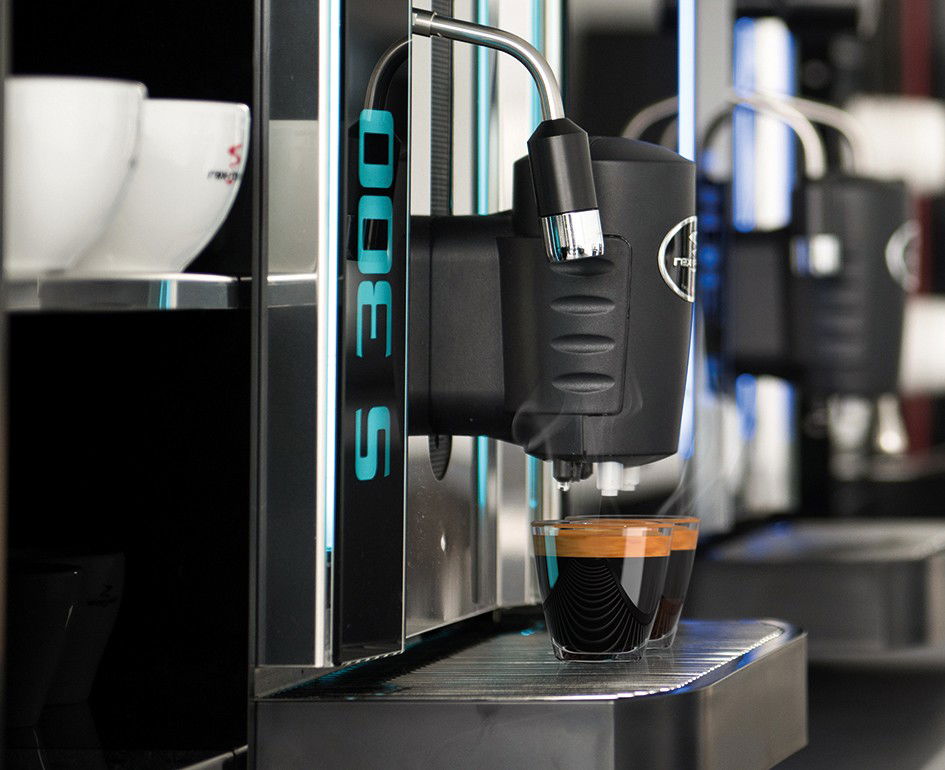
Sensors for the Perfect Coffee
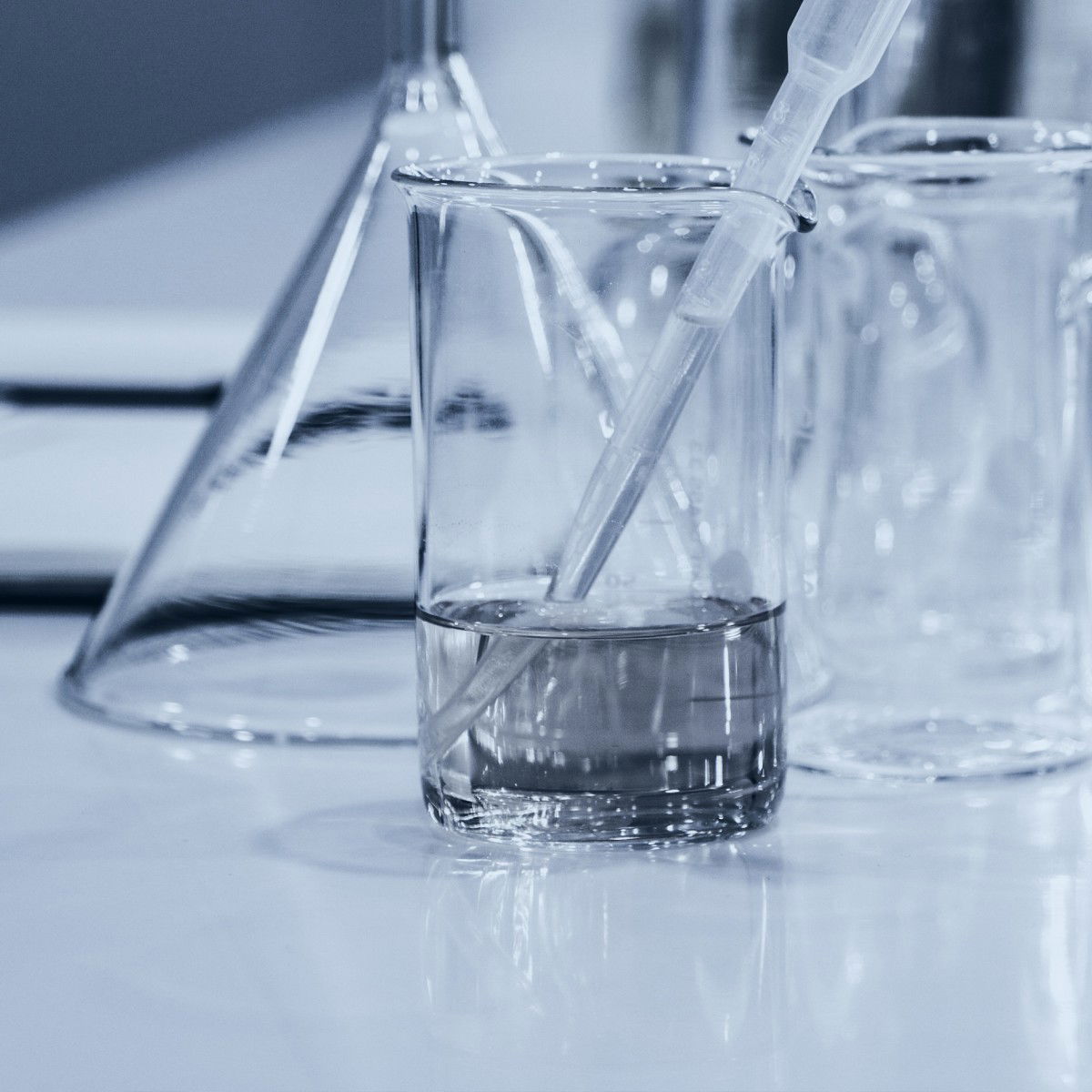
Other Chemistry, Food and Pharma Applications